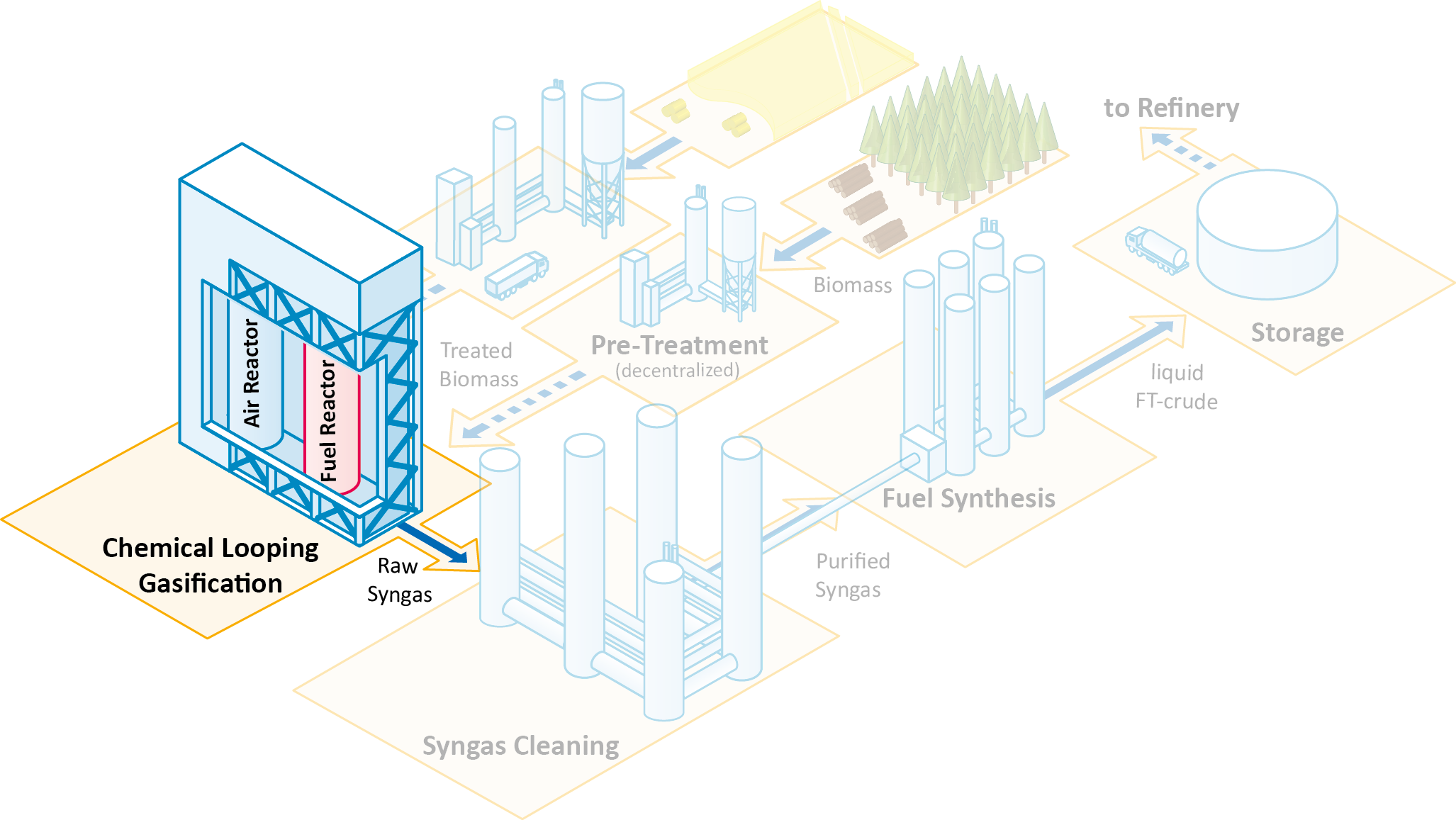
Chemical looping gasification (CLG) is used as innovative technology for gasification of solid fuels, such as biogenic residues. The reactor system typically consists of two coupled fluidized bed reactors, as illustrated in the figure. The oxygen required for the endothermal gasification reaction is provided by a solid oxygen carrier that is circulated between the two fluidized bed reactors. Metal oxides are typically used as oxygen carrier.
In the fuel reactor (fluidized with steam and/or carbon dioxide), the biomass is first devolatilized forming char (C), ash, and volatiles, mainly CH4, CO, H2, CO2, H2O, H2S, NH3, and higher hydrocarbons (tars). The char is gasified by steam and CO2 forming CO and H2:
C + H2O → CO + H2
C + CO2 → 2CO
If steam is available in large amounts, H2 is also formed due to conversion of H2O via water-gas shift reaction:
CO + H2O ↔ CO2 + H2
The gaseous products of devolatilization and gasification, i.e. mainly CO, CH4 and H2, are partly oxidized by a reduction of the oxygen carrier:
MexOy + CO → MexOy-1 + CO2
4 MexOy + CH4 → 4 MexOy-1 + CO2 + 2 H2O
MexOy + H2 → MexOy-1 + H2O
Volatile matter also reacts with the oxygen carrier by partial oxidation. Furthermore, the oxygen carrier can provide surfaces that catalyse the steam reforming reaction.
The gases leaving the fuel reactor will consist of a mixture of CO, H2, CH4, CO2, H2O. The latter compounds are unavoidable to fulfil the heat balance of the gasifier, but will be removed downstream.
The oxygen carrier particles leaving the fuel reactor with the syngas are separated from the gas (by means of a cyclone) and transferred to the air reactor (fluidized with air), where the reduced form of the oxygen carrier (MexOy-1) is re-oxidized to MexOy by the oxygen contained in air:
MexOy-1 + 0.5 O2 → MexOy
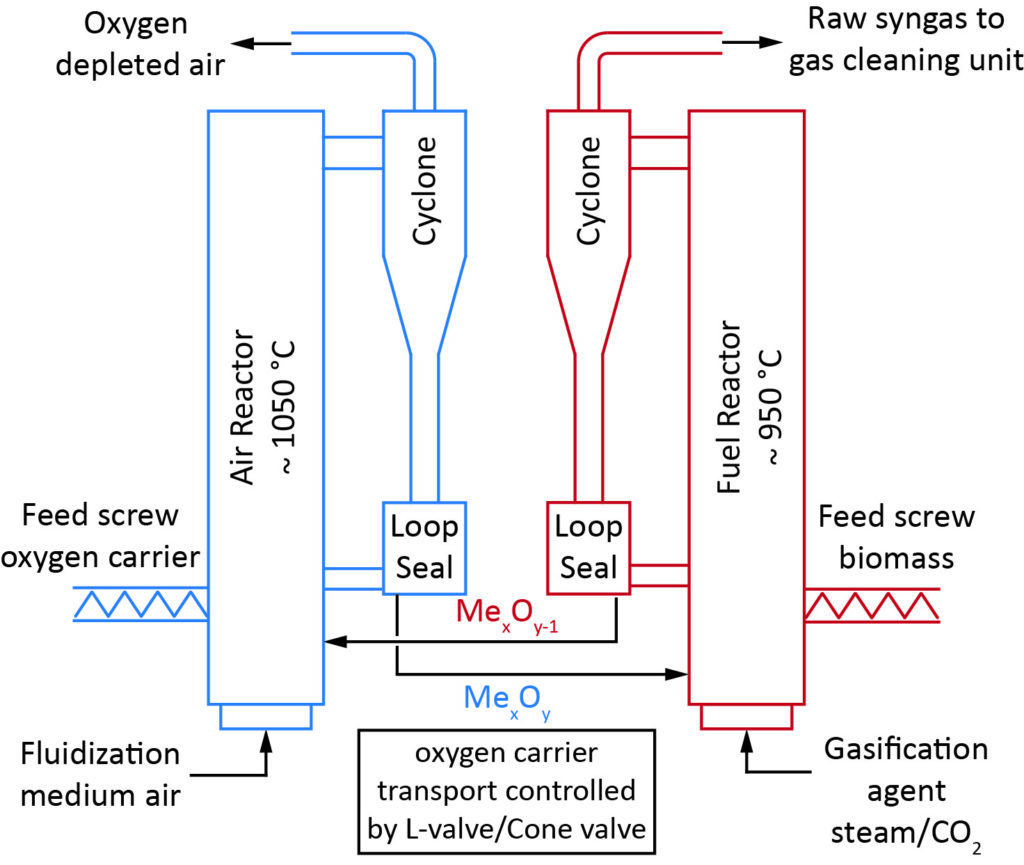
The oxygen carrier particles leaving the air reactor with the off-gas are separated from the gas (by means of a cyclone) and transferred back to the fuel reactor. The reaction in the air reactor is strongly exothermic, whereas the overall reaction in the fuel reactor is endothermic. In order to maintain the operation temperature of around 850-950 °C in the fuel reactor, heat is supplied by transfer of solids flow from the air reactor that is operated at higher temperature (~900-1050 °C) than the fuel reactor. Unconverted char leaving the fuel reactor may also be transferred to the air reactor and combusted there, thus providing additional heat in the air reactor. However, the ambition is to minimize this transfer rate (e.g. by using a carbon stripper) in order to keep the air reactor clean from fuel components. The solid mass flows between the two reactors could be controlled by a cone valve or an L-valve. The heat contained in the off-gases of the two reactors can be utilized for highly efficient steam/power generation with a very low degree of corrosion expected downstream the air reactor.
The reactors could principally be operated at either atmospheric pressure (avoiding the compression of air to the air reactor) or under pressurized conditions (avoiding the compression of the syngas). For large-scale commercial applications, a pressurized system could be of advantage due to the corresponding reduction in reactor size leading to a significant reduction in construction costs. Both options will be comparably assessed within this project.
The CLG process for biogenic residues has to be optimized with respect to conversion efficiency, selectivity, tar formation, operability, while at the same time taking into account specifications for the final usage of the syngas. These performance indicators are influenced by the feedstock properties as well as by the design and operating conditions of the reactors, i.e. temperatures, steam/carbon ratio, solids circulation, and particle residence time. The operating conditions are mainly determined by the properties of the oxygen carrier, the gasification and fluidization characteristics of the feedstock as well as the agglomeration and deposition tendency of the ash. The latter is a particular issue for biogenic residuals, such as straw, and requires a detailed understanding of the feedstock properties and process conditions. For example, high bed temperatures have the advantage of high conversion rates and low tar formation, but lead to an increased tendency towards ash agglomeration. An important issue for CLG is the selection of an appropriate oxygen carrier that has to fulfil several requirements, i.e. high reactivity towards hydrocarbons to yield CO and H2 high mechanical strength, low agglomeration tendency, and low cost. In addition, these materials should be environmentally benign, thus making Ni- and Co-based materials unsuitable. It would also be preferable if the oxygen carrier had a reversible interaction with important impurities, such as alkali. It is expected that certain Mn- and Fe-based materials could have such characteristics.