The importance of a proper cleaning of the syngas for the subsequent Fischer-Tropsch process and the treatment itself are described in Syngas Treatment. To ensure the compliance with the requirements, the syngas treatment will be tested in a test rig owned and operated by RWE Power.
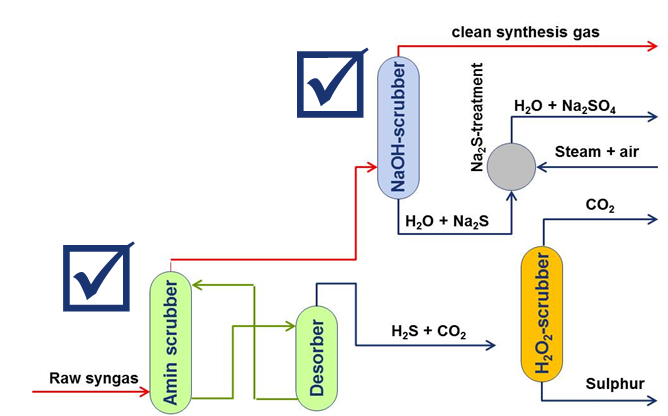
A scheme of the Test Rig’s process is provided in Figure 1. In the first step of the pre-cleaning, the raw synthesis gas enters an acid gas removal section composed by an amine scrubber and an amine regeneration column (desorber). The function of this section is to significantly reduce the sour gases CO2 and H2S and separate them from the raw synthesis gas. The pre-cleaned raw gas is sent to the caustic tower and the sour gases are derived to the H2O2 contacting section.
In the caustic tower, the pre-cleaned raw synthesis gas is washed with caustic soda (NaOH) and the sour gas content of the synthesis gas is reduced below 0.1 ppm. The caustic tower consists of two caustic and one water washing section. After the washing, the spent caustic soda is recycled through a caustic treatment system (Na2S-treatment).
The sour gas stream, leaving the scrubbing section as the overhead product of the amine regeneration column, is routed to the H2O2 contactor. In this section, the H2S contained in the CO2 is selectively oxidized under atmospheric pressure by H2O2 to sulphur which is separated by filtration from the H2O2 water solution. The H2S free CO2 stream is leaving the overhead of the H2O2 contactor where a part of the CO2 will be compressed and used as lock hopper gas in the gasification section.
The amin scrubbing is to be carried out by the 200 3/h-scale gas treatment plant at TU Darmstadt, while the RWE Power’s mobile gas rig will supply the caustic soda and the hydrogen peroxide scrubbers.
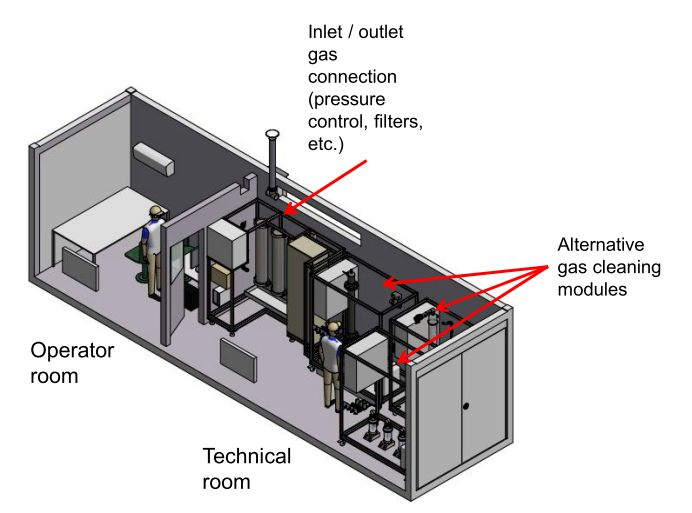
The mobile gas cleaning rig, illustrated in Figure 2, consists of three modules, which can be operated alternatively. It is mounted in a standard container which can be disconnected from utilities and transported to different operation sites easily.
The first module mainly contains three stirred glass reactors for basic investigation of ideal operation parameters (contact time, gas flow, solvent concentration, etc.).
The second module contains a glass column to investigate the real operation conditions using the results of the first module as starting points for optimization.
The third module consists of a pressurized steel column to be operated either with amine or with caustic solvent. As these solvents and process steps are well known, this module only serves for completion of the total cleaning process scheme if needed.